ALMC – GRAYSTAINES, NSW
Among the many storage system innovations at ALMC’s Sydney distribution centre (DC) are:
- Custom-made, heavy-duty UU-beams which support three pallets per bay and provide extra space for accessing picking stock within floor level storage locations
- A new type of heavy-duty carton live storage (CLS) system designed to handle cartons and pails
- An ultra space-efficient drive-in/drive-through pallet racking system
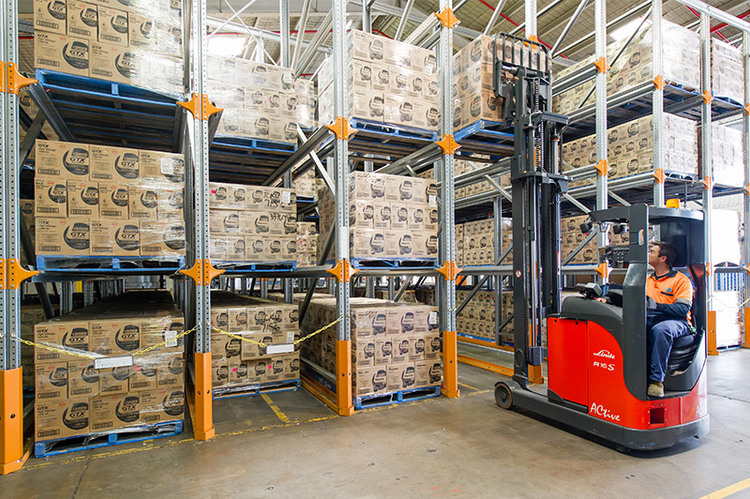
Transforming picking on the floor
When ALMC decided to upgrade outdated storage systems at its Guildford DC, a key driver was improving the safety and ergonomics associated with the manual handling of its product range, which includes heavy cartons and pails.
ALMC’s Facility Manager, Jackie Wall, said: “We wanted to eliminate a number of potential safety issues with our previous storage system configuration, and improve order fulfilment accuracy and productivity.”
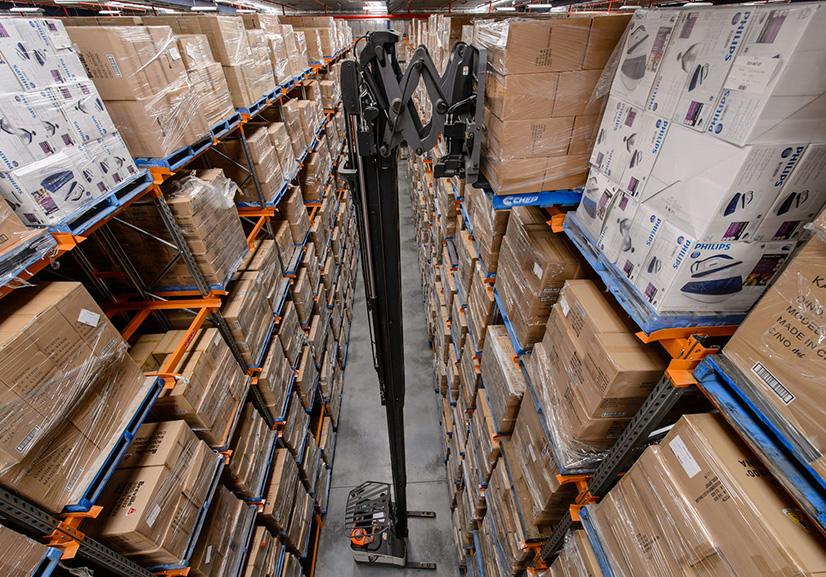
Working closely with ALMC and its business process consultant Portland Group, Dematic developed a range of innovative ColbyRACK storage solutions to improve distribution and order fulfilment performance, with special emphasis on improving access to stock and the safe handling of ALMC’s SKU range of around 1,500 products.
Smart racking design improves order picking ergonomics
“With fixed beam heights our old storage system was inflexible, which created ongoing product slotting, access and OH&S issues,” explained Ms Wall.
“A relatively low first beam level meant some of our taller staff would have to bend over when picking stock on pallets stored on the floor, and accessing stock at the rear of pallets required a lot of reaching, stretching and awkward product handling.
“This is not ideal when you are picking products weighing up to 20 kg, so improving access to stock at all of our ground floor pick slot locations was a key driver for our new storage system design,” she said.
“Dematic came out and reviewed our operation and came up with a number of storage system configurations for us to evaluate,” added Ms Wall.
“The solution we preferred was moving from the industry-standard two pallet-wide racking set-up, to a three pallet-wide configuration. Placing only two pallets on the floor within the new three pallet-wide bays creates sufficient space for our order pickers to be able to walk around the pallets when selecting goods. This significantly improves the ergonomics associated with the operation and eliminates the need for them to reach or stretch when picking. It also reduces the physical effort required in lifting our heavier SKUs, and has substantially improved the safety of our manual handling activities,” she said.
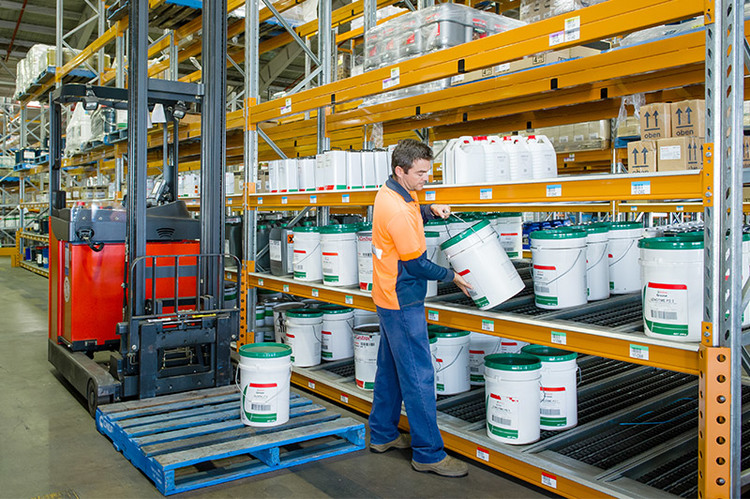
“By making the new racking three pallets wide and closely following the DC’s roofline profile, Dematic also managed to implement our new and much safer storage solution without adversely impacting our total pallet storage capacity.”
For more information on ALMC contact us today.
- The article was originally published on 16 March 2019