MURRAY GOULBURN – LAVERTON, VICTORIA
Murray Goulburn, Australia’s leading processor of milk and the country’s largest exporter of processed food, commissioned a Dematic RapidRunner high density storage system at its Integrated Logistics Centre (ILC) in Laverton in Victoria.
Combining the density of drive-in racking with the benefits of pallet flow, the RapidRunner system uses self-propelled “intelligent” carts to handle pallets within the storage system. The RapidRunner carts run on rails which pass under each pallet location on each level of the storage system.
Unlike other storage system layouts which require multiple access aisles, RapidRunner systems only require aisles for pallet entry and pallet retrieval, making them very space efficient.
Once satisfied that the RapidRunner concept was the best solution for Murray Goulburn, work commenced on what would be the first large scale facility in Australia.
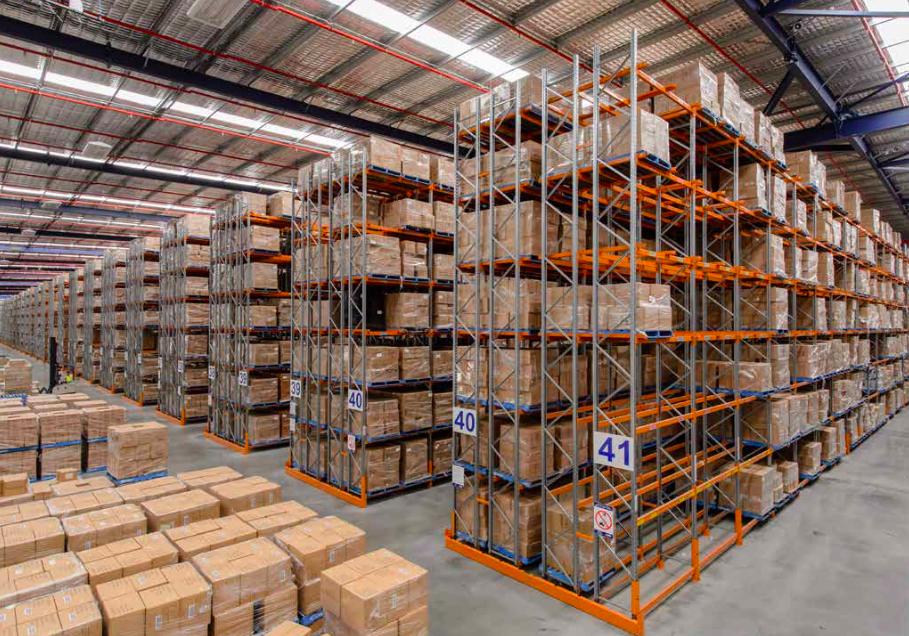
The RapidRunner concept offers excellent potential for manufacturers and companies that need to store large quantities of pallets of the same product to significantly reduce their storage and handling costs.
Phil Saunders, National Storage & Distribution Manager, Murray Goulburn
Because the RapidRunner carts operate automatically and independently within the system, forklift operators are free to focus on bringing product to and from the racking without the need to drive into the rack. The carts can be easily lifted out of one storage lane and transferred to another by a forklift, making it possible for a single cart to service multiple lanes.
As well as providing excellent space utilisation, the RapidRunner system enabled Murray Goulburn to handle double the throughput with less than half the operators it would require with any other type of storage system, such as Drive-In Racking.
Murray Goulburn installed nine RapidRunner carts, with three spares for back up, and for use during busy periods when increased throughput is required.
Customer benefits
- Combines the density of drive-in racking with the benefits of pallet flow
- Dramatically increase storage density
- Double the throughput with less than half the forklifts and operators
- Cost efficient as a single cart can service multiple lanes
- Facilitates pre-assembly and staging of orders
- Space efficient due to very deep storage
- Rapid unloading and loading of pallet
- Integration of RapidRunner carts into existing IT systems
ALMC – GRAYSTAINES, NSW
Among the many storage system innovations at ALMC’s Sydney distribution centre (DC) are:
- Custom-made, heavy-duty UU-beams which support three pallets per bay and provide extra space for accessing picking stock within floor level storage locations
- A new type of heavy-duty carton live storage (CLS) system designed to handle cartons and pails
- An ultra space-efficient drive-in/drive-through pallet racking system
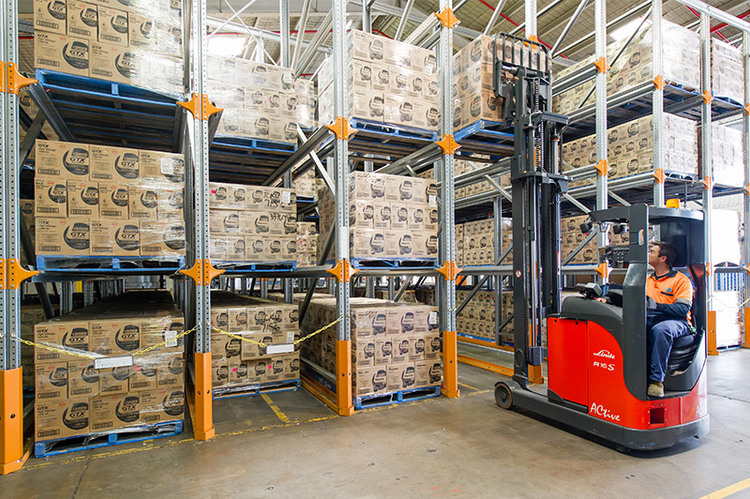
Transforming picking on the floor
When ALMC decided to upgrade outdated storage systems at its Guildford DC, a key driver was improving the safety and ergonomics associated with the manual handling of its product range, which includes heavy cartons and pails.
ALMC’s Facility Manager, Jackie Wall, said: “We wanted to eliminate a number of potential safety issues with our previous storage system configuration, and improve order fulfilment accuracy and productivity.”
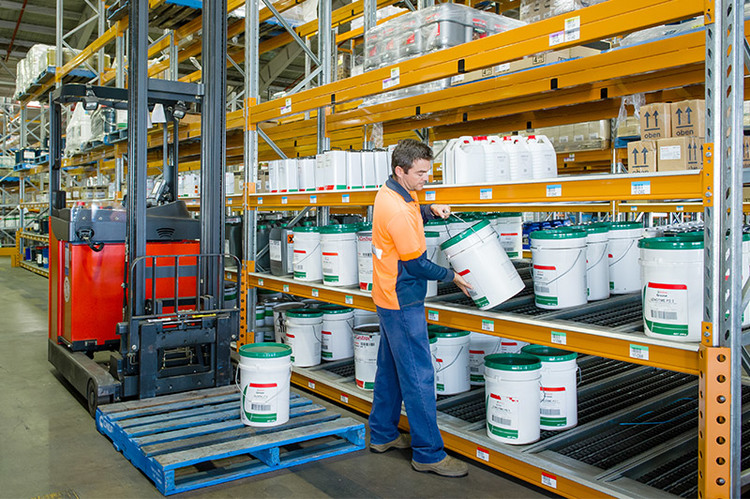
Working closely with ALMC and its business process consultant Portland Group, Dematic developed a range of innovative ColbyRACK storage solutions to improve distribution and order fulfilment performance, with special emphasis on improving access to stock and the safe handling of ALMC’s SKU range of around 1,500 products.
Smart racking design improves order picking ergonomics
“With fixed beam heights our old storage system was inflexible, which created ongoing product slotting, access and OH&S issues,” explained Ms Wall.
“A relatively low first beam level meant some of our taller staff would have to bend over when picking stock on pallets stored on the floor, and accessing stock at the rear of pallets required a lot of reaching, stretching and awkward product handling.
“This is not ideal when you are picking products weighing up to 20 kg, so improving access to stock at all of our ground floor pick slot locations was a key driver for our new storage system design,” she said.
“Dematic came out and reviewed our operation and came up with a number of storage system configurations for us to evaluate,” added Ms Wall.
“The solution we preferred was moving from the industry-standard two pallet-wide racking set-up, to a three pallet-wide configuration. Placing only two pallets on the floor within the new three pallet-wide bays creates sufficient space for our order pickers to be able to walk around the pallets when selecting goods. This significantly improves the ergonomics associated with the operation and eliminates the need for them to reach or stretch when picking. It also reduces the physical effort required in lifting our heavier SKUs, and has substantially improved the safety of our manual handling activities,” she said.
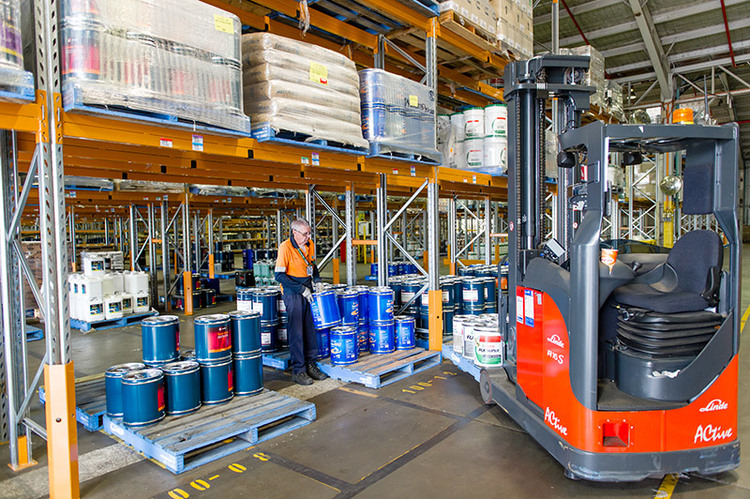
“By making the new racking three pallets wide and closely following the DC’s roofline profile, Dematic also managed to implement our new and much safer storage solution without adversely impacting our total pallet storage capacity.”
For more information on MURRAY GOULBURN contact us today.
- The article was originally published on 17 March 2020