Dematic has received an order for a ColbyRACK storage system purpose-built to deal with the forces generated by seismic events, together with a multi-level order picking module, conveyor sorting system and associated order fulfilment software from New Zealand’s largest grocery distributor, Foodstuffs South Island Ltd (FSSI), for its new 46,000 square metre distribution centre (DC) in Christchurch
While the new DC is essentially a Greenfield project, it will be physically connected to FSSI’s existing 13,000 square metre ambient DC at Hornby, which has provided centralised distribution to the co-operative’s members for the past five years. The Greenfield DC, which will also consolidate operations from FSSI Papanui DC in Christchurch, will have the capacity to store more than 40,000 pallets to a height of 10.7m, and is expected to begin distributing stock by the third quarter of 2014.
FSSI experience with seismic events
FSSI Hornby DC was one of more than 40 in Christchurch to suffer significant storage system damage during the 7.1 magnitude earthquake that struck Christchurch on September 4, 2010. Having been through the experience of dealing with a major rack collapse, we never want to go through that again,” said Foodstuffs Logistics Operations Manager Kris Lancaster.
Foodstuffs Logistics Operations Manager Kris Lancaster
“We were very fortunate that the earthquake occurred at 4.35 am and there was only minimal staff on the warehouse floor at the time.
“The DC was a total mess and would obviously be out of action for some time, so we immediately began implementing alternative distribution arrangements, including leasing some external warehouse space and increasing the role of other DCs in the FSSI supply chain network,” he said.
“FSSI then began researching what we could do to ensure if another earthquake of such magnitude were to occur again, that our storage systems would stand up to it.”
FSSI and Dematic
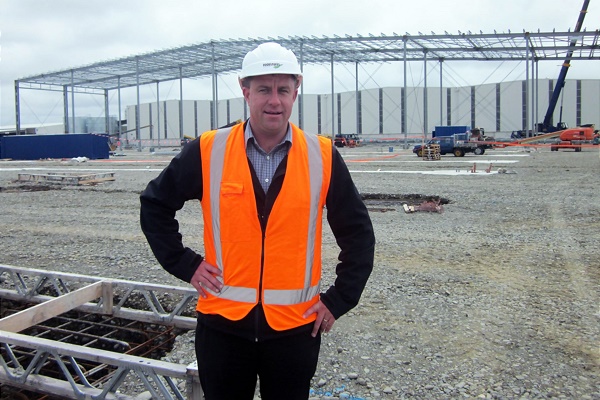
“FSSI had been working with Dematic on various real-time logistics and automated order fulfilment projects for several years, and we were aware of the sound reputation Dematic had gained for the structural integrity of its ColbyRACK pallet racking and associated storage systems,”
Explained Mr Lancaster
“Working closely with Dematic’s structural engineering team headed up by Dr Murray Clarke we came up with a new storage system layout that optimised the available footprint and airspace within our ambient DC.
“Dematic really pulled out all stops to push the project through as quickly as possible, and our new ColbyRACK system was designed, manufactured, shipped and installed at the Hornby DC in just over three months,” he said.
Following the installation of the new ColbyRACK storage system, the Hornby DC continued to experience many aftershocks from the September 4, 2010 earthquake, however its first real test came when another major seismic event rocked Christchurch on February 22, 2011. The 6.3 magnitude earthquake caused even more significant damage to the city than the September 4, 2010 earthquake, resulting in the death of 185 people and an estimated 15 billion NZ dollars of damage to properties.
“When the February 22, 2011 earthquake struck at 12.51 pm, our DC was in full swing, with many of our people on the warehouse floor at the time. Obviously, this was a pretty scary experience for everyone given that they had all seen the result of the previous earthquake less than six months prior,” said Mr Lancaster.
“However, despite this seismic event causing much more damage across the city than the September 4, 2010 earthquake, our new ColbyRACK system did the job it was designed to,” he said.
“The racking made a fair racket as it swayed to and fro and vibrated in response to the ground movement, but it stood up to everything the earthquake threw at it. We didn’t lose a single pallet, and a subsequent inspection by a structural engineer prior to our people re-entering the DC confirmed the storage system didn’t suffer a single component failure.”
“This was very reassuring for everyone in FSSI, especially for our people in the DC,” added Mr Lancaster.
“So when it came time to look at what we would do with storage systems in our new Greenfield DC, there was never any hesitation in selecting Dematic to fit-out the warehouse with a high-rise ColbyRACK system,” he said.
Storage system design in seismic areas
Dematic’s Structural Engineering Manager, Dr Murray Clarke, said it was vitally important to be involved right at the start of the project design process to ensure the safest pallet racking solution could be integrated into FSSI’s new DC.
“For example, the floor in the Greenfield DC is being constructed using post-tensioned concrete,” said Dr Clarke.
“Because of this it was critical that we worked in conjunction with the structural engineer to identify the location of the post-tensioning strands within the slab so that they would not conflict with the positioning of the racking system’s seismic baseplates, which are secured using chemical anchors,” he said.
Dr Clarke added: “Our seismic baseplates are designed to behave in a predictable manner in the presence of uplift forces and it is essential that their installation is not impeded or adversely impacted by the presence of other elements within the floor.”
Multi-level order picking module
In addition to supplying the Greenfield DC’s new storage systems, Dematic is also assisting FSSI with the implementation of a two-level split-case picking module incorporating integrated conveyors and voice-directed picking.
Controlled by Dematic’s PickDIRECTOR order fulfilment software, order totes will travel through the pick module by conveyor, automatically diverting only into zones where picks are required. Operators equipped with voice computers will batch pick singles and inners from thousands of longspan shelving locations into the order totes, which will then be conveyed to despatch where a 10 lane Dematic conveyor sorting system will automatically sort the totes for despatch, with the reusable totes doubling as the shipping container for orders.
Designing the interface between the existing and new DC
The multi-level pick module will span from the existing DC into the new DC. Because of this Dematic has designed the pick module as two separate interconnected structures with a sliding bridging plate.
Dr Clarke explained: “To cater for the fact that the pick module will be straddling the existing DC slab and the new DC slab, we felt it would be safer to split the actual pick module into two separate elements and connect them with a sliding bridging plate so that the structure can accommodate any differential movement between the two slabs.”
The impact of where goods are stored and pre-existing damage
“As well as supplying our new racking, Dematic has also provided us with invaluable advice about how the location of pallets of different weights throughout the racking can affect the performance of storage systems during a seismic event. To that end, we now have very clear guidelines regarding the weight limit of pallets within different levels and locations of our storage systems,” explained Mr Lancaster.
“Dematic also improved our awareness of the potential impact that any pre-existing damage to racking can have during an earthquake. To prevent any accidental damage at the ground floor pick faces, our new storage systems feature Dematic’s Colby Protect-a-RACK system, including front and rear upright guards and end-of-aisle protectors,” he said. “It is very reassuring for our warehouse staff to know FSSI is implementing world’s best practice storage systems to ensure their safety day in, day out.”
How storage systems respond to seismic events
When structural engineers design a building, they can make reasonable assumptions, guided by design standards, about the likely loadings on the structure during day-to-day use.
Warehouse storage systems, on the other hand, could theoretically be empty one day, and full the next. The total load, where loads are located and the height of racks all have a significant impact on the performance of a storage system during a seismic event.
In non-seismic areas, storage systems are designed to support mostly vertical loads – horizontal loads typically account for only around 0.5% of the vertical loads, making them relatively insignificant.
However, when an earthquake occurs, ground acceleration can increase the horizontal loadings on storage systems by a factor of 10 or more.
The storage system rack frames and beams respond by swaying to and fro, and the total mass within the racks – the stored pallets – begins to move in relation to the ground, creating inertial cross-aisle (transverse) and down-aisle (longitudinal) forces within the rack structure. The inertial forces acting in the cross-aisle direction will cause the rack to sway, increasing compression in one upright and decreasing the load on the other. The greater the horizontal seismic inertial forces acting on the storage system, the higher the compression and uplift forces will be. These uplift forces result in the racks attempting to pull the uprights’ baseplates free of the ground anchors, which secure them to the floor.
For more information about designing seismic rack please contact us today.
- The article was originally published on 1 November 2013